-
3Dプリンター
- 公開日:2022.6.22
- 更新日:2022.6.22
AM技術は製造業の革新的プロセス!メリットや種類を詳しく解説
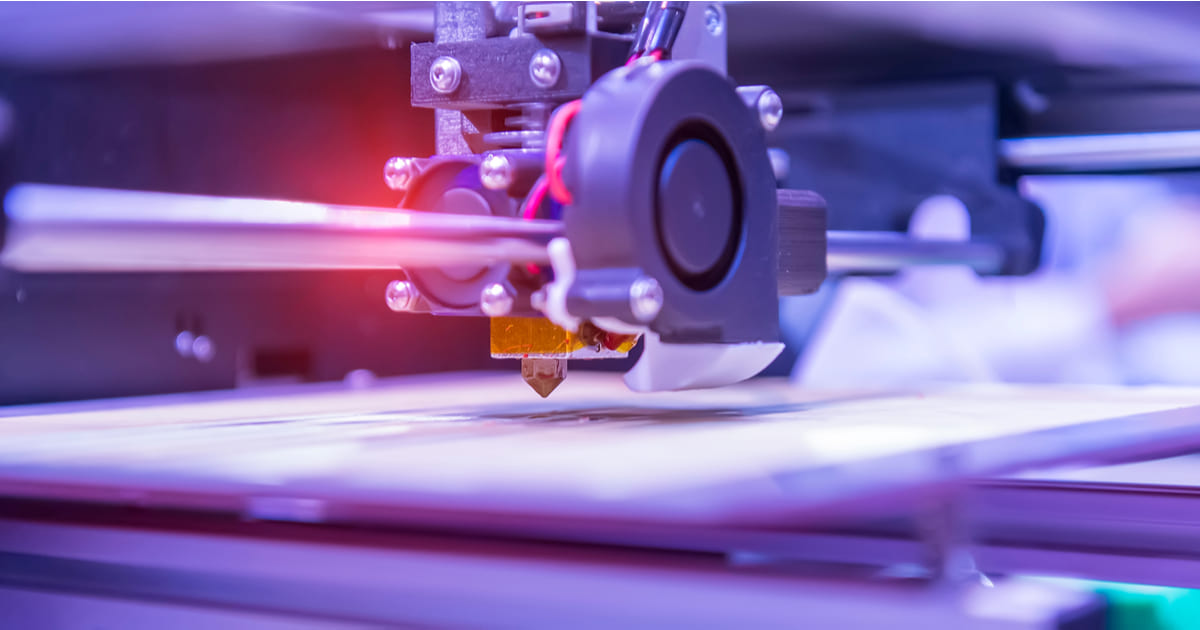
AM技術は、製造業をはじめとした幅広い分野における革新的プロセスです。すでに一部の企業ではAM技術を導入し、製品の実用化に成功しています。
本記事では、AM技術を活用するメリットや種類、企業の導入事例について解説します。
ページコンテンツ [非表示]
AM技術とは?
AM技術とはCADデータ(三次元データ)を基に、材料を付け加えながら製品を造形する技術で、AMはAdditive Manufacturing(付加製造)の略称です。
3Dプリンター装置で造形し、材料には樹脂や金属、セラミックスが用いられます。光源にはレーザーや電子ビームなどが使用され、材料を選択的に硬化・焼結(焼き固める工程)することで製品を作製します。
AM技術は従来、形状確認をはじめとした試作に使用されてきました。しかし現在では、複雑な形状も作製可能になり、材料ロスを削減できるため、本格的な製造技術として注目されています。
AM技術における7つの種類
米国試験材料協会(ASTM)が定めるAM技術の種類は、次の7つです。
- 結合剤噴射
- 材料噴射
- 粉末床溶融
- 指向性エネルギー堆積
- シート積層
- 光重合硬化
- 材料押出し
原料に樹脂を用いる場合「結合剤噴射」「材料噴射」「光重合硬化」などで造形可能です。
一方で金属の場合は、主に「粉末床溶融」と「指向性エネルギー堆積」が使用されます。最近では、後処理に手間がかからない「結合剤噴射」と「材料噴射」も用いられています。AM技術の特徴について、それぞれ詳しく確認しましょう。
結合剤噴射
結合剤噴射は、バインダージェッティングとも呼ばれるAM技術。樹脂や金属、セラミックスに適用可能です。3Dプリンター装置内で、プレート上に敷き詰めた粉末状の材料に対して、液体の結合剤(バインダー)をノズルから噴射します。
結合剤によって粉末を固めた後、プレートを一層下げて再び粉末を敷き詰めます。積層を繰り返し、すべての層を固化すると造形は完了です。ただし金属材料を用いる場合、結合剤を除去して強度を向上する必要があるため、焼結プロセスが欠かせません。焼結とは、金属の融点以下で焼き固める処理のことです。
結合剤噴射で得られた造形体の強度は比較的低いため、強度を必要としない小型品の試作に適しています。
材料噴射
材料噴射はマテリアルジェッティングとも呼ばれ、液状にした材料を噴射して、任意の形状に積み重ねながら造形する方式です。金属材料の場合、液状の金属は噴射後に冷却されるので、すぐに固まります。
一方で樹脂材料の場合、噴射された後も液状のまま残ってしまいます。そのため、光に当たると硬化する「光硬化性樹脂」を使用し、紫外線で照射することが特徴です。実用化に十分な強度が得られないので、主に試作で用いられる方法です。
粉末床溶融
粉末を敷き詰めた層(粉末床)に対して、レーザーや電子ビームで溶かしながら造形する技術が「粉末床溶融」で、パウダーベッド溶融とも呼ばれます。一層ごとに粉末の敷き詰めと溶融・凝固を繰り返し、最後に造形体の周りにある粉末を取り除く造形方法です。
取り除いた粉末は、ふるいにかけて再利用できるため材料ロスを防げます。粉末床溶融では複雑な形状を高精度で造形できるため、航空機のタービンブレードや噴射ノズルなど、実用化を考慮して使用されています。
指向性エネルギー堆積
指向性エネルギー堆積はノズルから粉末を噴射したり、ワイヤーを供給したりしながらレーザーまたは電子ビームを照射し、溶融・凝固させて造形する方法です。高速で造形できるうえ、2mを超える大型製品に適用できるメリットがあります。
以前はタービンブレードの補修などに使用されましたが、近年は複雑形状も作製できるようになり、航空宇宙分野における大型製品への適用も検討されています。
シート積層
シート積層は、約0.2mm程度の金属箔や紙、シート状の樹脂を何層も積み重ねる造形方法です。接着方法の違いにより、2種類に分類できます。紙やプラスチック、樹脂を原料にする場合は、接着剤を使用してシートをつなぎ合わせる「積層製造方式」です。
一方で金属を原料にする場合、超音波を使ってシートを接着する「超音波結合方式」を用います。シート状であれば様々な材料に適用でき、シート積層後に機械加工をしやすい特徴があります。
光重合硬化
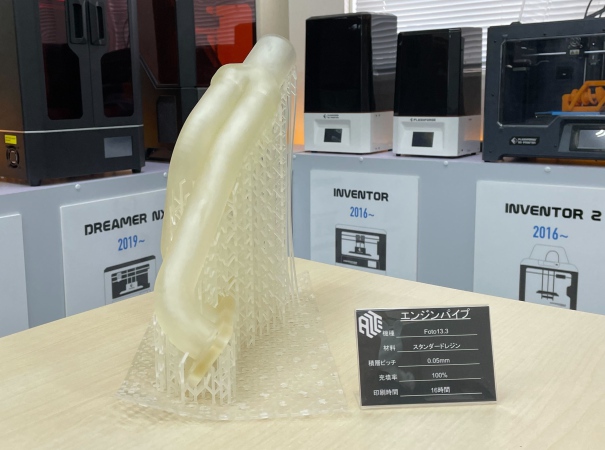
光重合硬化は光造形とも呼ばれ、液状の硬化性樹脂を容器に溜めておき、紫外線やレーザーを照射しながら造形する技術です。光に当たった樹脂のみ硬化するため、選択的に照射することで、自由に製品形状を制御できます。
一層の照射・硬化が完了後に造形プレートを容器の中に沈め、次の層の造形を行います。複雑な形状でも滑らかな表面に仕上げられ、0.1mm程度の精度で造形可能です。
材料押出し
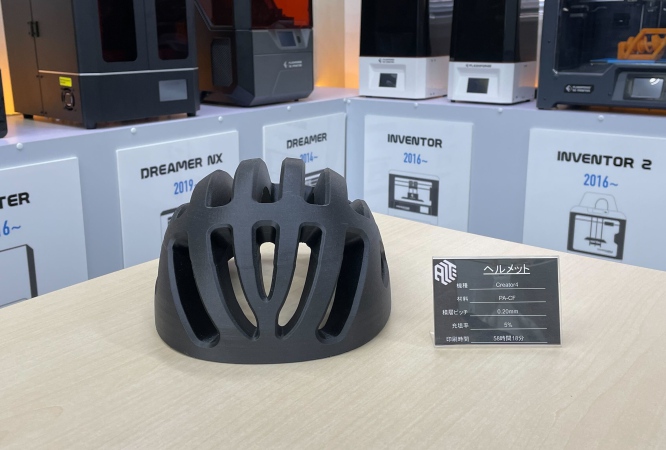
材料押出しは、ワイヤー状の熱可塑性樹脂を熱で溶かす方法のため、熱溶解積層とも呼ばれています。熱可塑性樹脂は加熱すると軟化し、冷却によって固化するため、熱で形状を制御できる樹脂です。
溶かした樹脂をノズルから押し出して、造形プレート上に積層して造形体を作製します。主に試作品の造形に用いられ、少量生産に適した技術です。熱溶解積層方式による3Dプリンターの詳細を知りたい方は、こちらの記事もご覧ください。
<<【参考記事】3Dプリンターとは?活用事例を交えて仕組みや使用方法について簡単に解説
AM技術のメリット
AM技術を活用するメリットは、次の4つです。
- 複雑形状が作製可能
- 材料ロスが少ない
- 在庫管理が不要
- 輸送時間やコストを削減
それぞれの特徴を確認し、AM技術のメリットを理解しましょう。
複雑形状が作製可能
AM技術を活用すると、従来では製造できない複雑な形状でも作製可能です。
従来の鋳造プロセスで金属材料を製造する場合、溶かした金属を「鋳型」と呼ばれる容器に流し込み、金属が冷えて固まった後、切削により任意の形状に仕上げます。固化した材料の表面を削って成形するプロセスのため、内部を空洞にするといった複雑な加工はできません。
しかしAM技術では、必要な箇所に材料を付け足すプロセスのため、切削は不要です。中空形状やメッシュ構造でも簡単に造形できます。
材料ロスが少ない
材料ロスが少ないことも、AM技術のメリットです。従来の切削加工では、切削くずは再利用できないため廃棄されます。AM技術では、製品重量分の材料のみで造形できるため、材料ロスを最小限に抑制可能です。
実際にアメリカの総合電機メーカーGE社では、航空機部品にAM技術を適用し、材料ロスを最大90%削減しています。
在庫管理が不要
AM技術に必要なものは、材料とCADデータのみです。金型を使用する大量生産とは異なり、金型や大量の材料を管理する必要がありません。そのため在庫管理の手間が削減できるうえ、3Dプリンターを設置するスペースがあれば、大きな工場も不要です。
輸送時間やコストを削減
AM技術では必要分の原料のみ保管し、CADデータに基づいて造形できるので、大量の材料を準備する必要はありません。したがって、工場から生産された材料を輸送する時間やコストを削減でき、効率よく生産できます。
AM技術の課題
様々なメリットがあるAM技術には、以下3つの課題があります。
- 造形体の特性が不十分
- 高精度化が必要
- 造形ノウハウが必要
それぞれの課題について、内容を理解しましょう。
造形体の特性が不十分
AM技術における課題の一つは、造形体の特性が実用化レベルに到達しにくいことです。
例えば粉末床溶融で造形する際、造形パラメータが適切でなければ粉末の溶融・固化が不十分となり、空隙(欠陥)が発生する可能性があります。
空隙が含まれている造形体は、密度100%の製品に比べて、強度をはじめとする特性が劣ってしまいます。そのため実用化されている製品は限定されており、さらなる普及のためには特性を向上させる造形パラメータの開発や、造形後の熱処理改良が必要です。
高精度化が必要
AM技術の高精度化も、実用化に求められる課題の一つ。造形体の精度は「寸法誤差」や「表面粗さ」が指標になります。造形体の寸法精度は±0.1mm程度であり、高い再現性で製品を造形するためには、さらなる高精度化が必要です。
また表面粗さは最小5µmまで実現でき、製品として使用する際は、研磨で平面を滑らかにするケースがあります。ただし、中空部や微小部分は工具が届かないため研磨できず、造形直後の状態で使用されるので、表面粗さの向上が求められています。
造形ノウハウが必要
AM技術では、材料や形状に適した造形パラメータの設計が大切です。
例えば適切に造形パラメータを設計すると、内部に空隙が少ない造形体を作製できます。これらの造形パラメータは装置や材料、形状によって大きく変わるため、製品ごとに造形ノウハウを蓄積する必要があります。
またプロセス中に、造形体が倒れないように支える「サポート」を設計する場合もあり、後処理で取り除きやすい強度に制御することも重要です。
AM技術を導入する企業と事例紹介
AM技術を導入している企業と、具体的な事例を紹介します。
GEアビエーション
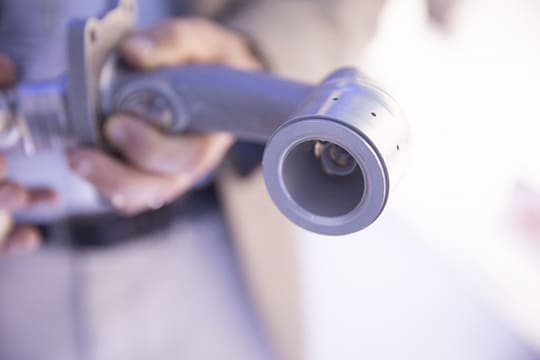
アメリカの航空機エンジンメーカー「GEアビエーション」は、2016年に3Dプリンターのメーカー「コンセプトレーザー社」を買収し、AM技術を積極的に活用している企業です。燃焼ノズルを3Dプリンターで作製し、航空機エンジンへの実用化に成功しています。
燃焼ノズルは複雑な形状のため、従来のプロセスで製造することは難しく、以前までは20個以上の部品を溶接・ろう付けにより組み立ててきました。
しかしAM技術によって部品の一体化に成功し、組み立ての手間やコストを削減しています。
DMG森精機
工作機械メーカー「DMG森精機」は2022年3月に「アディティブマニュファクチャリング Laboratory & Fabrication(AM Lab & Fab)」を設立し、受託加工サービスを開始。AM技術を試したい顧客の要望に応えて造形するほか、金属用造形コンサルティングも実施しています。
導入する3Dプリンターは「粉末床溶融」と「指向性エネルギー堆積」の2種類で、様々な原料や形状に対応できることが特徴です。
AM技術に関するよくある質問
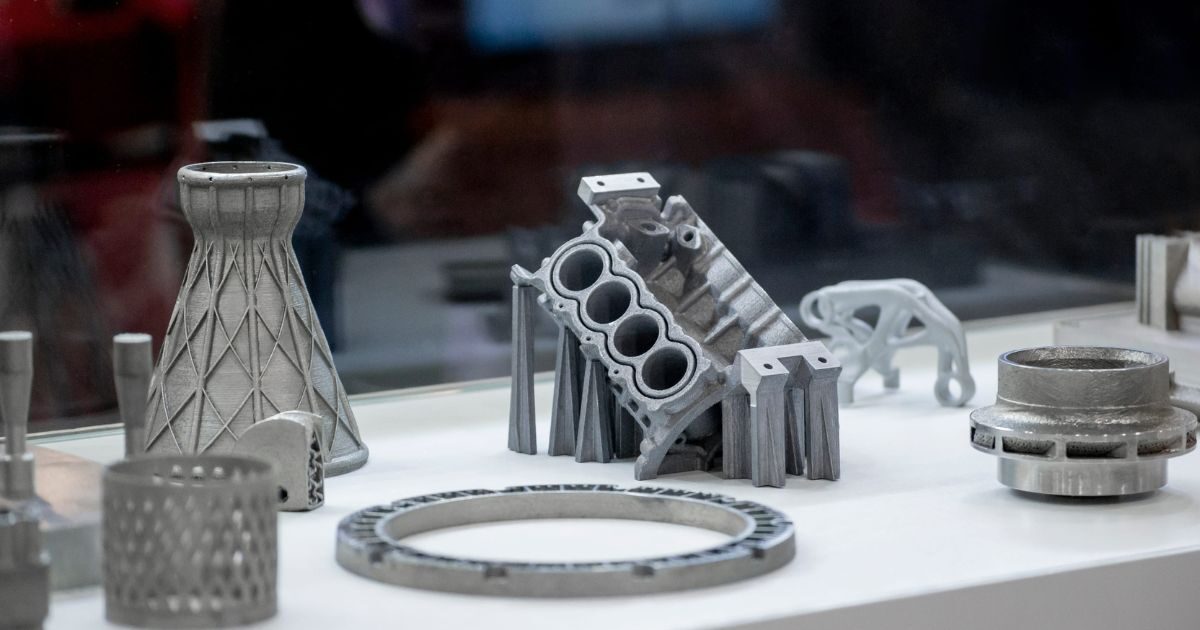
最後に、AM技術に関するよくある質問を紹介します。
AM技術の主な用途は?
AM技術の主な用途は、身近なものではフィギュア作製や展示品などです。実用化を考慮した用途には、医療分野や航空分野が挙げられます。
金型を使用した大量生産とは異なり、AM技術は多品種少量生産に適しています。またCADデータを適宜修正しながら、各用途で求められる形状に合わせて造形可能です。
そのため医療分野では、患者によって形状が異なる「歯列矯正用のマウスピース」や「人工関節」の用途に使用されています。
AM技術に使用できる材料は?
AM技術に使用できる材料は金属や樹脂、セラミックスです。ただし材料の種類によって、造形性に影響を及ぼす場合があります。例えばFLASHFORGEが提供するフィラメント(樹脂)を使用すると、金属やセラミックと比較して、簡単に造形が可能です。
FLASHFORGEのラインナップを一部、紹介します。
- PLAフィラメント:悪臭が少ないエコ素材PLA(ポリ乳酸)フィラメント
- ABSフィラメント:日用品や雑貨の造形に適したABS樹脂
- HIPSフィラメント:ABS樹脂向けのサポート材
高品質フィラメントの詳細を知りたい方は、こちらの記事をご覧ください。
まとめ
AM技術は金属や樹脂、セラミックスなど、多くの材料に適用できる技術です。材料の在庫管理を削減して複雑形状も作製できるメリットを活かし、3Dプリンターを活用する企業が増えています。ただし金属用の装置は導入コストが高いため、手軽に活用したい方は樹脂用3Dプリンターがおすすめです。
FLASHFORGEでは、光重合硬化(光造形)や材料押出し(熱溶融積層)の3Dプリンターを提供しています。AM技術を使ってみたい方は、お気軽にご相談ください。